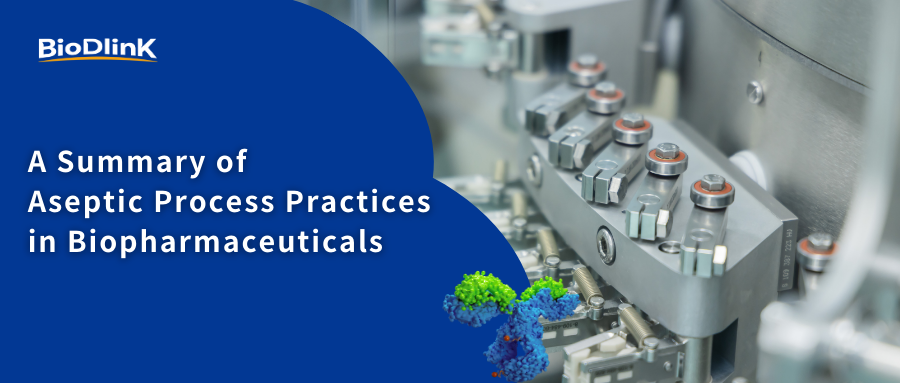
In recent years, with the explosive growth of
biopharmaceuticals such as antibodies,
fusion proteins, and ADCs, research into their production processes has
become increasingly in-depth and extensive. Aseptic production processes run
throughout the entire biopharmaceutical manufacturing process, especially in
the aseptic production of the final product. The key focus of our control over
aseptic production processes lies in the various details and the practical steps
involved.
As the final step in the biopharmaceutical GMP manufacturing,
sterile preparation filling requires personnel with professional expertise and rigorous
training, highly automated equipment that operates smoothly, sound design, and
strict standards to ensure the quality of the final product. A high-standard
aseptic assurance system runs throughout the entire complex, continuous
production process.
First:
Requirements for Personnel
For the manufacturing of sterile drugs,
personnel are the greatest source of contamination.
Article 20 of the "Good Manufacturing
Practice for Pharmaceutical Products (2010 Revision) Annex 1: Sterile
Pharmaceutical Products" (hereinafter referred to as "New GMP Annex 1:
Sterile Pharmaceutical Products") clearly stipulates: "All personnel
working in the clean area (including cleaners and equipment maintenance
workers) should be regularly trained to ensure that the operation of sterile
pharmaceuticals meets the requirements.
1.1
Personnel training and personal hygiene
1.2
Good behavior standards in clean areas
1.3
Clothing management and changing confirmation
Second:
Requirements for Materials and Consumables
In the production process of sterile
pharmaceuticals, materials, as excipients or raw materials, are an important
part of the drug. Their control over microbial limits and endotoxins is crucial
in ensuring the drug meets the established quality requirements. Key
consumables, particularly those that come into direct contact with the drug, also
play an important role in controlling particles and microorganisms. Below, two
aspects will be discussed: release testing and pre-use treatment control of
materials and consumables.
2.1
Quality standards and release testing of materials and consumables
2.2
Pre-use treatment and control of materials and consumables
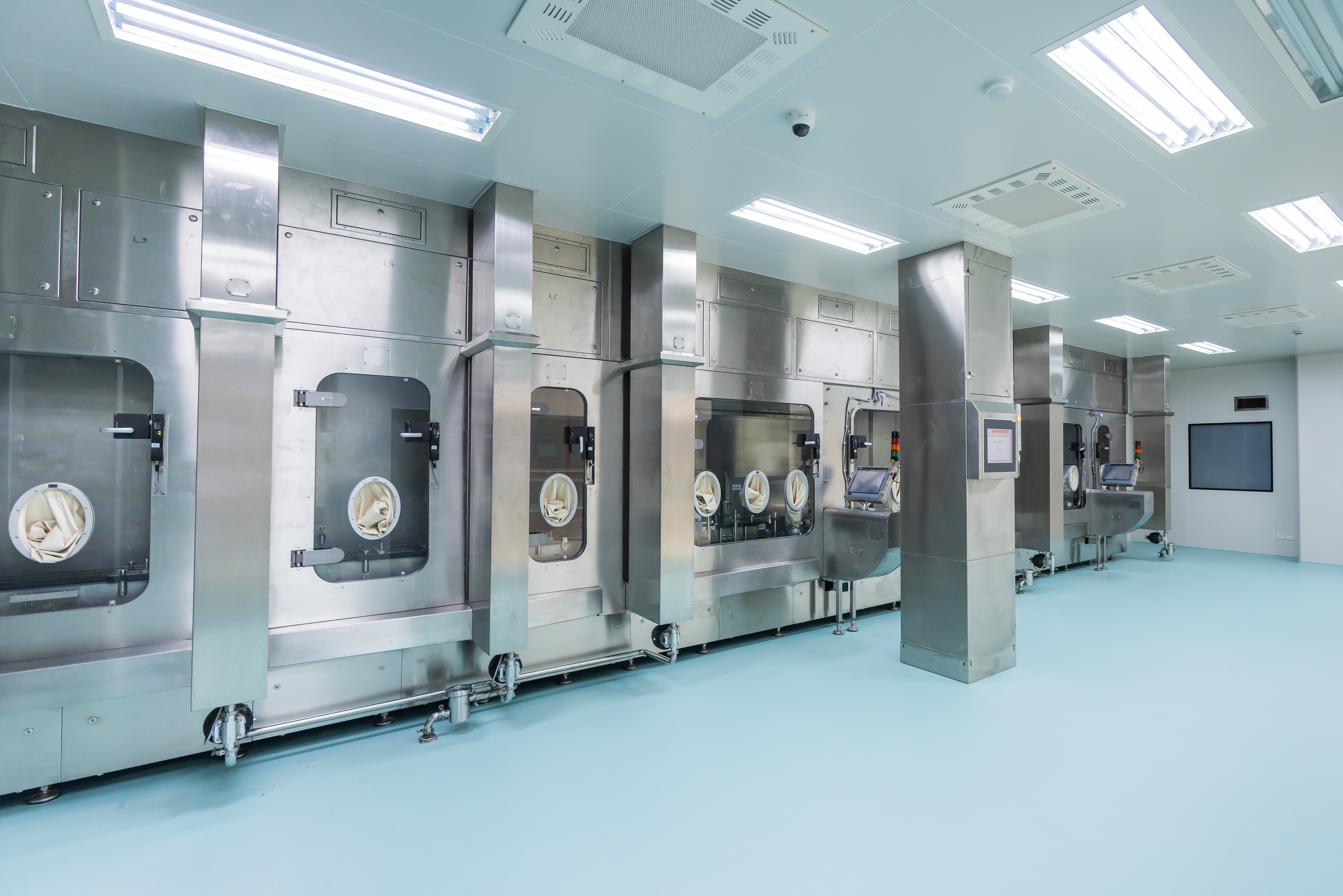
Third:
Equipment-Related Requirements for Aseptic Control
For sterile preparation production, process
equipment is one of the most important factors for aseptic assurance. The
performance of the equipment itself and any malfunctions during operation can
have either a positive or negative impact on aseptic production. The following
discusses the control requirements for equipment in sterile preparation
production from three aspects:
3.1
Equipment selection and design
3.2
Equipment maintenance and repair
Fourth:
Requirements for Plant Layout and Design
There are multiple provisions in
"Chapter 7: Plant” of the New GMP Annex 1 - Sterile Pharmaceutical
Products, which stipulate that for the production of sterile pharmaceuticals,
the plant must meet specific functional and layout requirements. This ensures
that the production environment of sterile pharmaceuticals complies with GMP standards
and meets the needs of drug production. The following discusses the basic
compliance requirements for sterile pharmaceutical production in terms of plant
layout and design:
4.1
Plant layout
4.2
Plant design
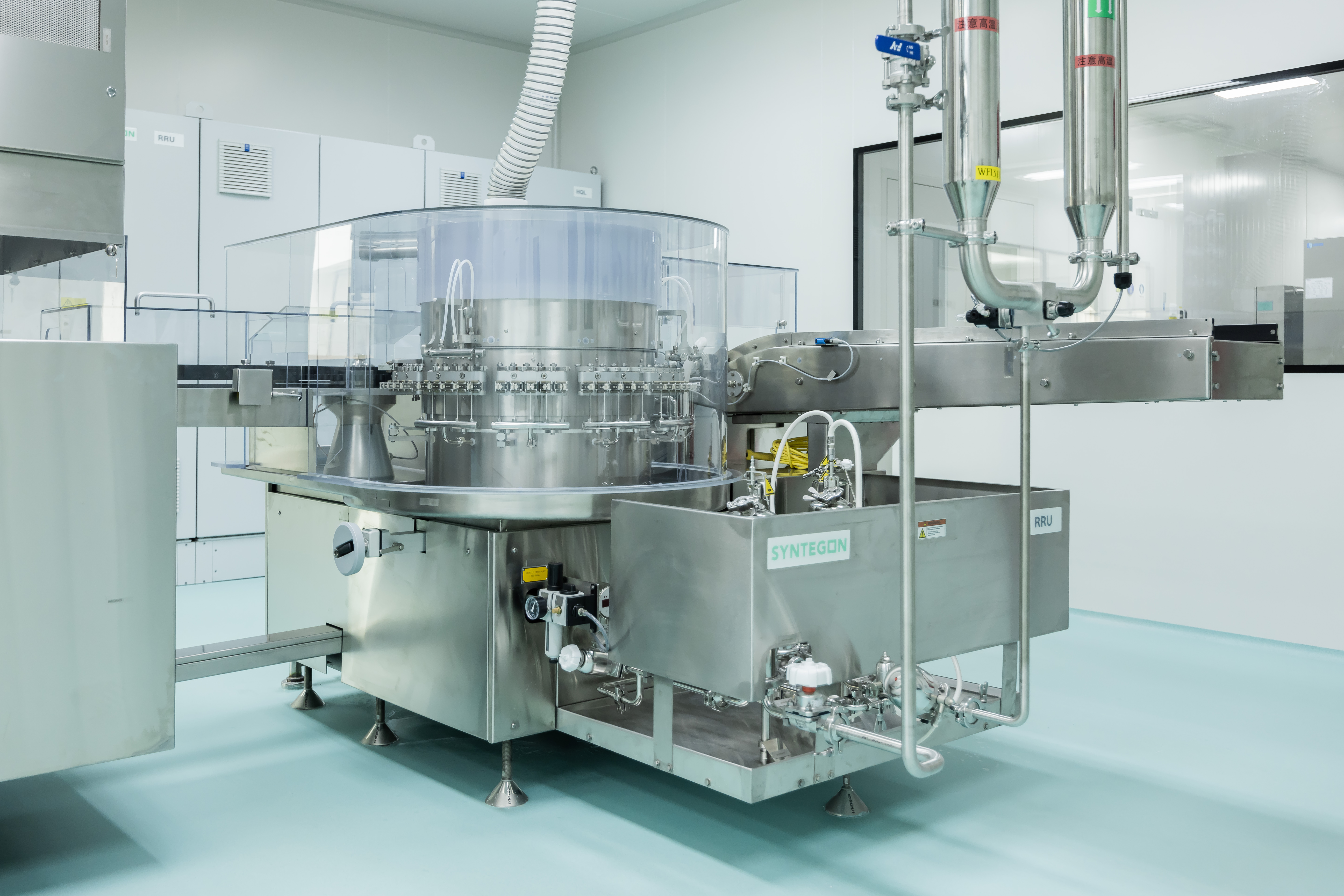
Finally:
The Role of Aseptic Process Design in Aseptic Assurance
Aseptic process design plays a critical role
in the aseptic control of biopharmaceutical production. A well-designed aseptic
process ensures a high level of aseptic control during production. Below, the
role of aseptic process design in aseptic assurance are discussed from two
aspects:
5.1
Sterilization filtration and aseptic filling process design
5.2
Aseptic process simulation (APS)
In addition to the above control measures, a
good aseptic production process also requires employees to continuously summarize,
optimize, and improve from the daily practice. Continuous improvement can only
be achieved by identifying risks during production and formulating
corresponding corrective actions.
For more questions on aseptic manufacturing
processes, please visit the official website of BioDlink or contact us.